Direct MCH®
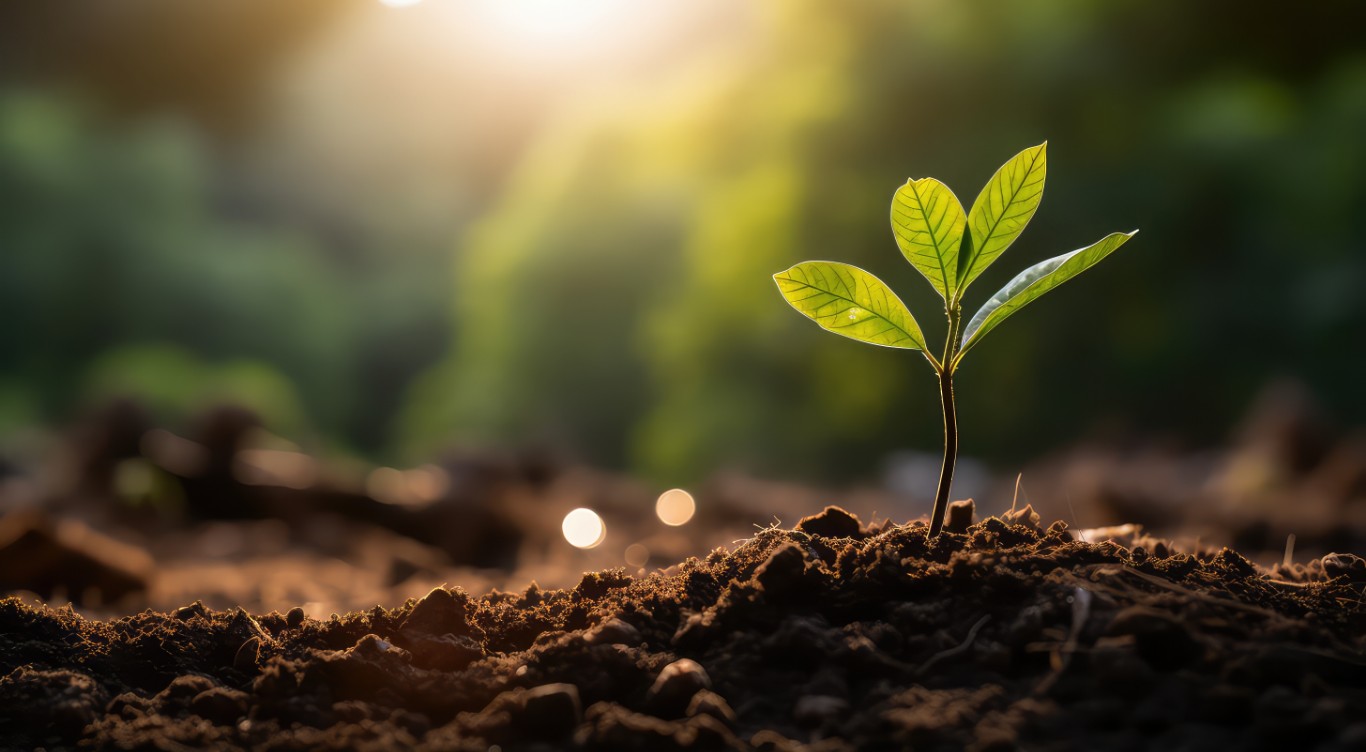
Direct MCH® operating principle and research and development
A schematic diagram of the Direct MCH® process is shown in Fig. 1. Oxygen is generated at the anode (left side) by electrolysis of water and toluene is converted to methylcyclohexane (MCH) at the cathode (right side). Although a complex process up to now, Direct MCH® enables MCH to be produced by a simple process with only an electrolyzer.
The key performance indicators in this process are current density (reaction rate) and Faraday efficiency (reaction selectivity). Improving these indicators can reduce facility costs in MCH production and lower hydrogen costs.
At ENEOS, we are working to improve these performance indicators by developing electrode catalysts, controlling the macro and micro structures of the catalyst layer and diffusion layer, enhancing the design of the electrolyzer structure, etc.
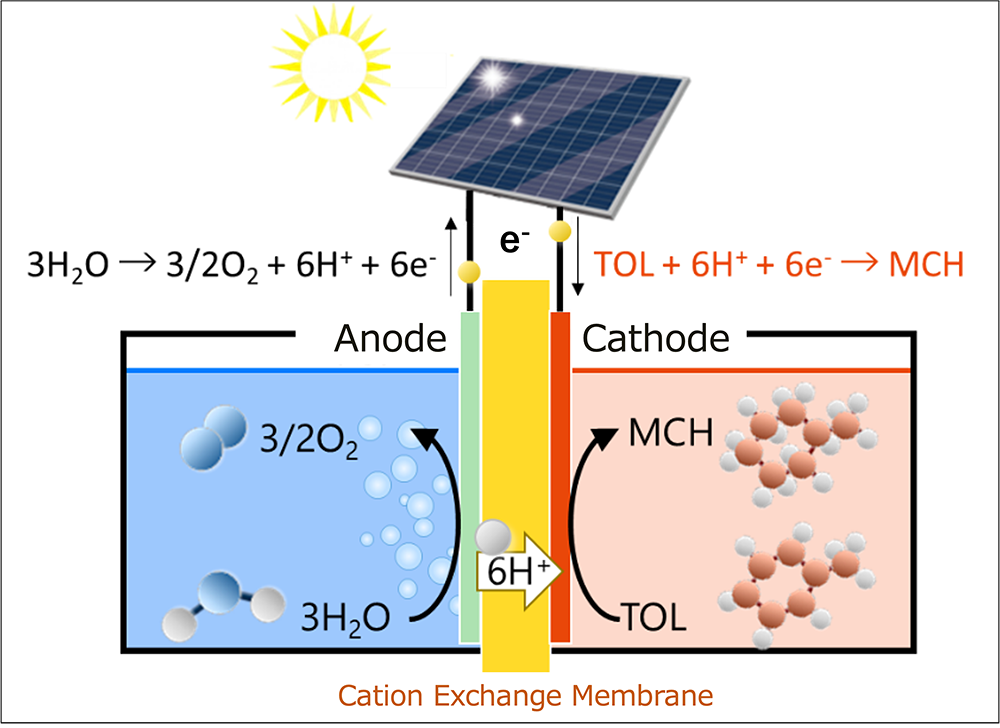
Scaling up the electrolyzer toward social implementation
We are working to scale up the electrolyzer and conducting technology demonstrations in Australia in phases toward social implementation of Direct MCH® (Figure 2).
In 2022, we successfully developed a 150 -kilowatt-scale medium-sized electrolyzer with electrodes equivalent in electrode size to those of commercial equipment. We are currently developing a larger-sized megawatt-scale electrolyzer, which is the minimum unit of commercial-scale.
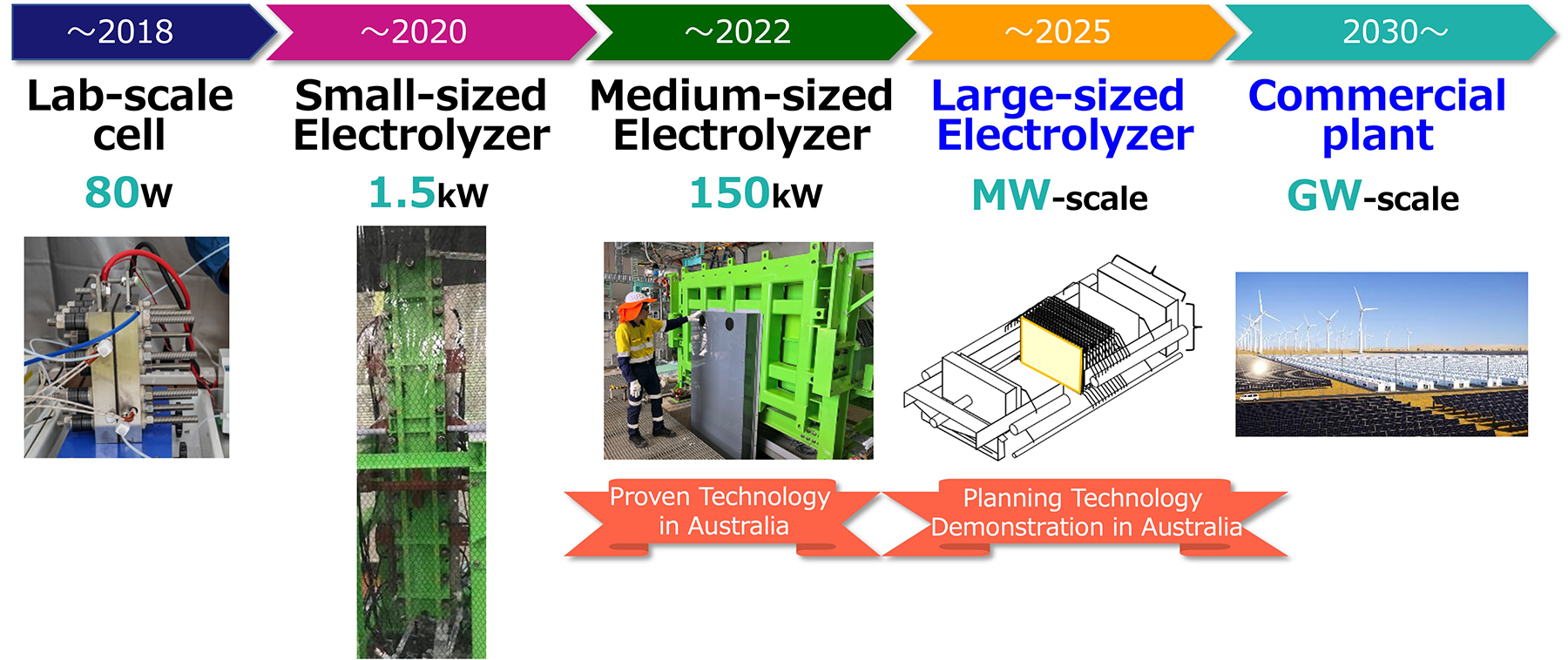
Process development toward social implementation and technology demonstrations in Australia
In 2022–2023, we conducted technology demonstrations of green hydrogen supply chains using the Direct MCH® process in Australia, where renewable energies are abundant.
Specifically, we constructed a 150 -kilowatt-scale Direct MCH® electrolyzer demonstration plant with a 250-kilowatt solar power system in Brisbane, Queensland, and conducted operation tests.
The opening ceremony for this plant was attended by the Queensland deputy premier and ministers and attracted much attention locally.
In operation testing, we investigated a green MCH production method linked to renewable energy and extracted problems in electrolyzer operation in a subtropical area. Part of the produced MCH was transported to Japan and hydrogen extracted from the MCH used to fill up a fuel cell bus at a ENEOS hydrogen station for test runs.
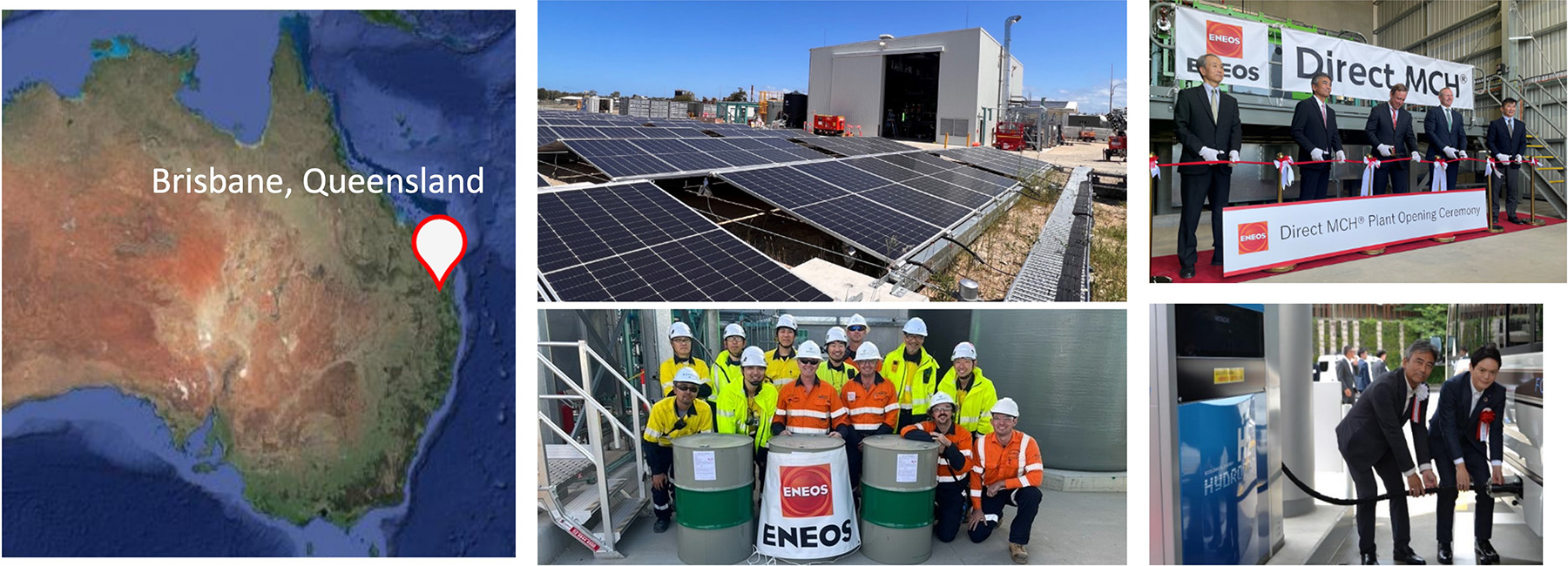
Two technologies supporting CO2-free hydrogen supply chains
—Direct MCH® and MCH-FCTM—
Regions where large amounts of renewable energy can be “harvested” are distributed unevenly around the world, so there is a need for developing technologies for transporting energy produced from renewable energy.
At ENEOS, we are researching and developing hydrogen carriers for efficiently transporting green hydrogen (CO2-free hydrogen) produced from renewable energy.
One such hydrogen carrier is MCH, which is a liquid that adds hydrogen to toluene. It can be used to transport 500 times more hydrogen than hydrogen gas at one time. MCH can also make use of the existing petroleum infrastructure such as large oil tankers and storage tanks so that early establishment of green hydrogen supply chains can be expected.
At ENEOS, we are developing technology for raising the efficiency and lowering the cost of MCH production (Direct MCH® described above) on the upstream side of this green hydrogen supply chain and technology on the downstream side (MCH-FCTM). Please see this page for information on MCH-FCTM.
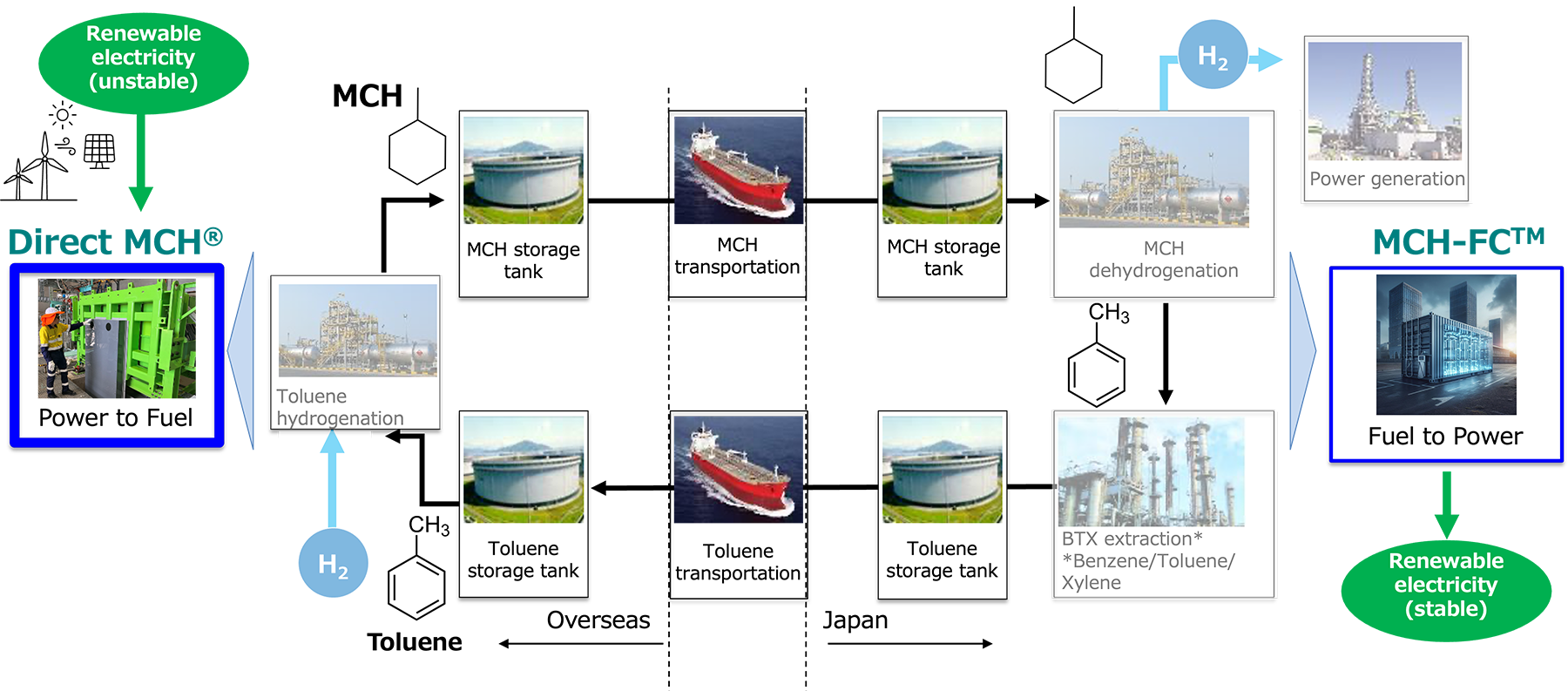